|
A number of the photos can be clicked for a larger version |
Following some friendly 'goading' by David Mulligan on a winter's evening in the Summit Inn, David Doyle set about contacting a fellow fisherman whom he knew had the talent to construct a brand new Howth Seventeen.
The savings fund of 25,000 gathered from the sale of the two boats 'Erica' and 'Isobel' had been put away for such an eventuality and though it would barely be enough to complete the build, the class knew the extra money would be raised from 'somewhere'.
|
Building the Hull
Boatbuilder Charlie Featherstone of Wicklow commenced the build in 2004 in between his normal day jobs of shell fishing and carpentry.
However the pressures of other jobs eventually ground the work on the new boat from a periodic trickle to a complete halt.
|
|
In October 2007 the Hull is taken to Peter Courtney's House
In October of 2007 the hull (comprised of frames, keel and stem made of oak and planks of larch) was transported to Howth, kept under the cover of Peter Courtney's 'boathouse'.
(This is actually a fine tent to the side of his house and workshop which could happily accommodate two Seventeens).
Photo opposite:
Hull arrives at Peter Courtney's 'boathouse'
|
|
Discussions to'd and fro'd during the AGM of November 2007 and the Spring Meeting of 2008 as to how the project could be completed. Charlie Featherstone had (generously) agreed to charge 10,000 for his work and the discussions centred on how the final jobs of making the decks, coaming and keel could be done.
It was not until Ian Malcolm took 'Aura' to the Classic Boat Regatta on Loch Derg in September of 2008 that the next step was taken. Ian was introduced to shipwright Dougal McMahon whose portfolio included many of the 'local' Shannon One Designs and he had also applied his skills to the decking of some Dragons.
Building Committee formed to complete the Task
A building committee was hurriedly put together comprising the class captain Brian Turvey, Ian Malcolm, Roddy Cooper and Peter Courtney. Dougal surveyed many of the Seventeens on their moorings after an Autumn League race in Howth one Sunday and following a quotation to build decks, coaming, rudder, attaching the lead keel and deadwoods - the committee agreed to give him the task.
He would endeavour to begin the work early in January 2009 and thought it might be completed in 2-3 months providing the keel be delivered to him towards the end of his work.
|
The Hull is taken to Dougal McMahon's Workshop - January 2009 |
So on the Saturday in January following the New Year, Brian accompanied Eoghan Ryan (aka 'Rocket') and his son Harry, with the new boat in tow, on the trip to Dougal's workshop in the sublime setting of Belmont Mill in County Offaly.
Rocket's four-wheel-drive Nissan Navara was to become the unofficial transport vehicle for the new boat thanks to his generosity and enthusiasm for the class. (Rocket and Shane O'Doherty had purchased 'Pauline' during the 2008 season).
|
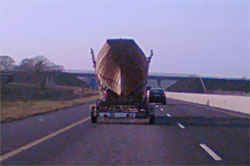
En route to Belmont, Co. Offally
|
|
|
Belmont Mill in County Offaly
|
Dougal's work on a 'Shannon One Design'
Dougal McMahon's skills are usually applied to the construction of the 'Shannon One Design'- a class specifically designed to sail in the fresh water of the Shannon and Lough Derg.
|
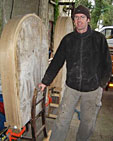
Dougal McMahon
|
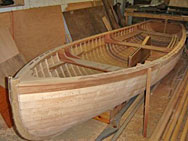
Shannon One Design
|
Work in progress on the decking in Dougal's yard.
The decks are constructed of pine with a kingplank and guardboard of Iroko while the coaming is constructed of steamed oak.
The decision to ask Dougal to do this work would prove to be inspired when we saw his magnificent completed work.
|
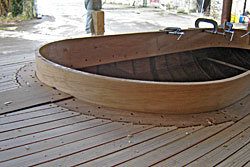
The decks and coaming in place
|
Making the Keel
Making the keel would now become the pressing issue and Brian was not short of suggestions as to how it could be done, but who would do it? True to character, Peter was confident that he had a design for a mould that he had discussed with engineer Brian Murphy and with help from the class captain (and possibly one other helper), it could be made in his workshop (the old basement kitchen in his home in Balscaddan).
|
The keel plug was retrieved from Charlie Featherstone's garden in Wicklow and some splits in the wood were repaired using some filler. (It was the same plug that had been used to form the mould for the keels for Isobel and Erica during their build in 1987). It was sanded and primed before the mould was constructed around it. The first task was to screw the plug to a plank of wood which would form a base for the frame to be built up from. A second length of wood (with the same dimensions - about 6½ feet long by 18 inches wide) was placed over the plug with its centre cut out so that it could be fixed to the plank below.
|
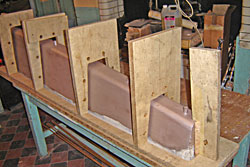
Keel mould frames in place around the wood
|
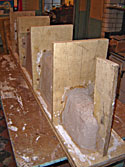
An inch thick layer of plaster is added
|
Brian and Peter then formed and fixed six frames around the plug, four of them like 'bridges' over the plug and two slotted at either end into the groove that would slot into the deadwoods under the hull. The mould itself would be made up of an inner layer of fine plaster and an outer layer of concrete mix bonded with 10mm reinforced steel bars running the full length of the frame. (3 each side). A webpage showing how concrete boats are constructed in the US inspired Peter to add layers of 'chicken-wire' within the concrete for extra strength. A cement mixer was hired and Ian joined to add some cement-mixing experience to the team.
The concrete was allowed to dry for a week before the mould frame incorporating the plug as turned back on its 'feet'. The mould had been carefully designed not to weigh much more than 250kg so that it could be lifted by about six people. When the plug was removed most of the inner layer made of plaster remained intact, though a few 'bubbled' areas had to be scraped and removed (with the metal tube attached to a hoover).
Hindsight would suggest that a 'finer' moulding plaster would have worked better than the coarser bonding plaster, but a few hours attention and refilling with a quick-drying filler finished the inner surface of the mould. Six 12mm core stainless tubes were inserted and fixed with caps where the keelbolts would later be fastened (W.H. Boyd's original specification of half-inch muntz metal was examined and its tensile strength was compared with that of stainless steel which was seen to be slightly stronger than the muntz). The tubes (and consequently the bolts) are slightly 'splayed' at the top of the keel mould to add 'rigidity' to its fastening to the hull. Two 12mm ringbolts were also added to either side of the approximated centre of balance at a distance believed to be the width apart of a standard pair of forks on a forklift truck.
|
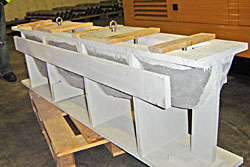
The keel mould is complete with eye bolts for lifting the lead
|
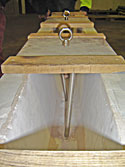
Stainless tubes for the keelbolts secured in the mould
|
The mould was lifted from Peter's workshop early one morning in March 2009 by six hefty association members and driven to Clondalkin where Paul Fitzharris of Metal Processors Ltd would oversee the pouring of the lead. Paul's foreman at the foundry explained that he would be adding 5% Antimony to the lead to add 'stiffness' to the keel.
|
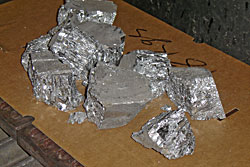
'Antimony' to be added to the molten metal
|
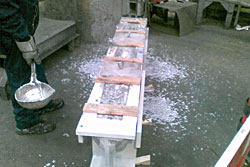
The lead is topped up after being poured
|
During this period the Seventeen Association met for their Spring Meeting and agreed that the request from Derek Bothwell to sail the new boat be granted and also that the boat be named 'Sheila' after the widow (Shelagh) of Norman Wilkinson who owned the boat 'Leila' from 1947 to 1999.
|
The lead was successfully poured and the keel (weighing 856kg) dispatched to Offaly with some 12mm threaded rod for the bolts.
Derek and Dougal then reviewed the keelbolt specification and calculated that the 856kg keel would require 781mm² of stainless bolts.
The 12mm bolts would only give 678mm², so Derek got a new lot of 16mm rod for Dougal to drill and fix.
|
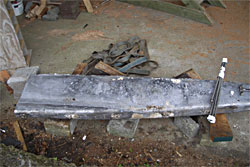
The completed keel
|
During the later completion of 'Sheila', such over- specification would become commonplace - strengthening many aspects of Boyd's original design in the obvious belief that the designer had not realised how long his boats should be made to last!
|
The Hull, complete with decks and rudder fitted, transported to Howth to complete the project
With the decks and coaming complete and the keel, deadwoods and rudder fixed to the hull, 'Sheila' was then transported back to Peter's tent in Howth for finishing. Brian was anxious to complete the remaining tasks as soon as possible and immediately set a 'launch date' of 23rd of May, allowing just four weeks to complete the boat.
Ian would make the gaff and topspars and donate an older spinnaker pole given to him by Brendan Cassidy, he and Roddy had already done most of the work to complete the mast and Paddy Cronin would make the boom from a length of spruce acquired from Dougal's stock of wood in Offaly.
|
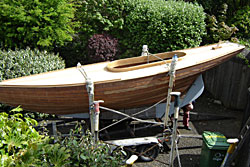
Back to Howth for another 750 hours of work
|
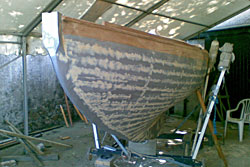
The painstaking filling and sanding begins
|
Then the hull was painstakingly caulked by local carpenter Gerry Levins, a task that took a full week - much of the time crouched under the hull tapping the cotton caulking thread into the seams between the planks. He filled and sealed over the cotton with brown putty leaving the hull prepared for the arrival of the finishing team.
The hull and decks would be prepared and finished by a team that included Brian, Derek, Roddy, John Curley, Hugh Walsh, David Doyle and crew Carla, Luke Massey, Peter Courtney, Dermot Mowatt, Pat Murphy and Harry McCormack.
The initial task of fairing the hull proved difficult as many of the larch planks had a darker grain which would stand proud following a sanding - some areas were better than others, but it was agreed that once the wood had absorbed the moisture from the sea, it would change much of its shape and as a consequence a 'truer' finish would be achieved in the years to follow.
Indeed, after the final gloss-coat on the topsides was completed, a week of torrential rain facilitated the expansion of the planks that squeezed a lot of the caulked putty out.
Derek used an electric plane to smooth the excess from the lead keel to ensure a smooth join with the wood around it. Following advice from a visiting David Harte, he took the corners off his plane which allowed a smoother finish. He also weighed the 6 kgs of shavings that he took away!
Dermot found a small plank of Iroko that had been used for fittings for 'Isobel' and took it home to make the deck cleats. A fortuitous donation of part of a hardwood window frame by Paddy Cronin (who explained that it had come from the 'Massey' home) inspired Neville Maguire to make a tiller for the boat.
Derek undertook the making of the bowsprit which was carved from a decking post bought at Grange Builders Providers - the iron cap fitting was donated by Peter and as one of the shackle holes had been damaged, David Doyle welded it shut and redrilled it to its original shape.
Four 6mm stainless steel chainplates were designed for shrouds and runners - all to be the same size and specification spanning three planks with a 10mm hole in the top one and 8mm holes underneath - the hole for the shackle would also be 10mm.
It was also decided at a later stage that the tiller cheeks could be made to the same design and so they were, though in the rush to get them, Connolly Engineering in Fairview could only supply 10mm stainless - they should last a while!
|
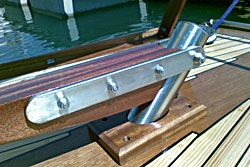
The rudder cap and tiller cheeks
|
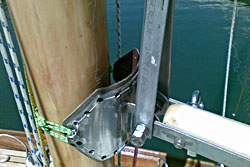
Gaff Jaws (leathering by Neville Maguire)
|
Other stainless fittings such as spiderbands, gammon iron/ bow roller, bowsprit fastener etc. were ordered from Wilmore Engineering in Kilmainham.
With regard to the rudder post, Hugh Walsh obtained a tube of 2¼ inch diameter stainless steel from a company in Baldoyle Industrial Estate and got a chrome cap (from Leslie Reynolds Ltd.) that fitted perfectly!
|
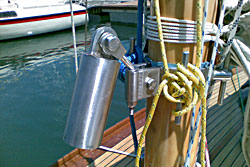
Mastband and spinnaker pole cup
|
Once the bilges and underdecks fore and aft were sanded and primed the cockpit area was give a liberal coat of 'Deks Olje'. Paddy cut the mast-hole in the deck (4½ inches diameter to fit the 4 inch mast) as well as the mast step groove and delivered the boom with a stainless plate epoxied into the mast end as a gooseneck fitting. He also designed and had organised the making of the gaff-jaws at the same time as making a set for Bryan Lynch's 'Echo'.
The fact that the hull planks were riveted right to the outer edge made it difficult to hide them in the varnished topplank - it would have been better if they could have been sunk deeper into all the planks and plugged. It also restricted the amount of fairing that could be done, though there were no complaints about that!
9 Days to the launch date
With 9 days to go before the launch, it was time to start getting the layers of varnish on the decks, but the never-ending rain was a serious concern. However, following a coat of varnish each evening it was discovered that it would be dry by noon the following day - the airy conditions within the tent were obviously allowing it to dry despite the damp and temperatures hovering between 8 and 12 degrees Celsius. The sixth coat was applied the night before the boat was delivered to Howth Yacht Club and it proved to be the one we were waiting for!
Seamus O'Carroll's generous donation of a hardwood bed headboard for the seat was seized by Derek who had an instant solution to a project at home involving the restoration of a grandfather clock. Derek had already earmarked other wood for the seat and would measure it using a seat borrowed from Jane and Michael Duffy's 'Hera'. Jane did the gold leafing on the new pale blue transom and added to the latest trend of displaying the year of completion. The transom would read in a Times New Roman typeface:
|
Michael had also offered to reconstruct the 'bottle smashing device' that had been constructed for the launch of Erica and Isobel 21 years earlier.
The Taoiseach of that time, Charles Haughey, had insisted that the bottle was guaranteed to smash, otherwise he might not launch the boat.
Thus in one last 'uber-spec', Michael recreated his industrial masterpiece of design which was to prove to be 'well up to the task!'
|
|
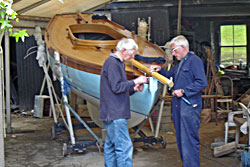
The bowsprit is fitted
|

'Sheila' emerges from the tent with the assistance of Luke Massey
|
'Sheila' transported to HYC past the home of the boat's designer
On Thursday May 21st the boat was hauled in her cradle (donated by Ian Malcolm whose 'Aura' is now stowed on her own road trailer designed by engineer Brian Murphy) from Peter's tent onto the class's own road trailer.
This was then brought to Howth Yacht Club where the mast and rigging were fitted for its display prior to launching.
It is estimated that it took about 750 hours of work to finish the boat from the time it was delivered to Howth 5 weeks earlier.
|
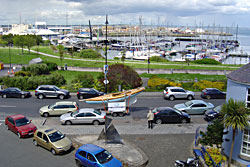
'Sheila' makes her way to HYC passing Sean O'Dwyer's sculpture of a Seventeen outside the home of the boat's designer W.H. Boyd of Howth House
|
'Sheila' Rigged & Ready for Launch Day
|
|
|
|